- Intuitive design delivers reliable, premium performance without complexity
- Built-in connectivity to InduSuite software applications optimise productivity
To improve weld quality and productivity in heavy industrial welding applications, ESAB has launched its next-generation Warrior Edge 500 CX multi-process power source, RobustFeed Edge CX wire feeder and Exeor MIG torches to global markets. The Warrior Edge system makes it possible for regular welders to achieve excellent welding results without a complex set-up process. It also has built-in connectivity and comes with a subscription to the InduSuite WeldCloud Fleet online software application. RobustFeed Edge CX also features a new digital gas control technology called TrueFlow that improves welding quality, saves gas and helps avoid weld defects caused by improper flow rates.
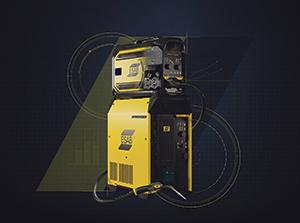
“The Warrior Edge platform checks all the boxes that will help our trusted partners in the global heavy industrial market grow,” said Flavio Santos, Vice President & General Manager, Global Equipment Solutions, ESAB Corporation. “It uses future-proof technology, simplifies training, promotes continuous weld quality improvement and enables connectivity to InduSuite digital applications that optimise productivity.”
The Warrior Edge 500 CX has a rated welding output of 500 amps at 60% duty cycle for synergic MIG/MAG/flux cored, pulsed MIG, MMA, gouging and Live TIG. It features the company’s next-generation digital control electronics for more controlled arc starts and greater arc stability to minimise spatter. It is designed specifically for the heavy industrial fabrication, structural steel fabrication, transportation, railcar, mobile equipment, tank and vessel fabrication and power generation industries.
InduSuite applications such as WeldCloud Fleet and WeldCloud Productivity revolutionise shop fabrication workflow with real-time insights across welding operations. They connect data, machinery and processes to optimise performance and unlock a shop’s true potential. WeldCloud Fleet enables users to manage welding jobs across a fleet of equipment at one or multiple locations, saving hours of time. It delivers support for planning, documenting and providing reminders for service maintenance and calibration activities; provides remote software upgrades and prepares event logs for early detection and notification of equipment issues.
Faster control, less spatter
Warrior Edge can detect and react to arc behaviour in critical moments, such as clearing of a short circuit, up to 10 times faster than traditional inverter machines. As a result, the system minimises weld spatter and creates a stable arc and more controllable weld pool. Operators find it easier to make better welds and spend less time grinding, both of which improve productivity. The new power current control module also enables ESAB engineers to develop, optimise and update each welding method independently.
“The digital current control in the Warrior Edge platform enables continuous process improvement and development without the need for hardware updates,” says Arne Lagerkvist, Global Product Manager – Heavy Industrial Welding Equipment, ESAB. “Warrior Edge gives users the confidence of buying a future-proof system.”
Simpler, more Robust
To further simplify operation, the RobustFeed Edge CX feeder locates material selection and configurations inside the case. Day-to-day settings, which include three ‘quick job’ buttons to recall pre-programmed weld parameters, are all managed on the clear and easy-to-understand front panel interface to allow for effective operation. Inside the feeder, a TFT LCD interface allows for menu based, clear text and intuitive interaction in the user’s native language.
RobustFeed Edge features an effective and quick to set-up operator management system that uses an RFID-reader to scan operator badges. This allows locking parameter limits for the quick jobs, improving repeatability and adherence to Weld Procedure Specifications.
The new TrueFlow digital gas control technology offers a level of precision, confidence and savings not previously possible to achieve with external pressure regulation devices. The system automatically prevents insufficient gas flow and optimises flow during arc starts and welding, a common source of quality issues and gas waste. It can save €600 to €1,200 per year in typical use cases.
RobustFeed Edge builds on the proven ESAB RobustFeed platform, which won the prestigious 2021 Red Dot Award for product design. The RobustFeed platform features SpoolSafe, a unique-in-the-market IP54 protection against dirt/dust that keeps wire dry and clean, improves feedability and reduces risk of weld contamination. RobustFeed Edge also includes the reliable PreciDrive wire drive system that maintains precision wire feeding performance to promote consistent weld quality.
RobustFeed Edge CX works with ESAB’s new Exeor torch, which features a slim, balanced lightweight design with soft grip area. Remote function buttons on the top of the torch enable adjustments without an additional cable. The torch is available in both air and water-cooled versions. Both provide superior cooling performance even at high parameters, further improving operator comfort and extending consumables life. An LED light illuminates the welding area prior to arc start.
T +44 (0)1992 768515
info@esab.co.uk
www.esab.com